Design and Manufacturing Processes
3D printing has taken on an important role in medical technology, as it enables complex anatomical structures and components for medical devices to be produced quickly and precisely. One example of the use of 3D printing in medical technology is the production of patient-specific orthoses that are perfectly customised to the patient's individual anatomy. Anatomical prints can also help with the customisation of implants. The research group is also investigating other manufacturing processes such as silicone moulding for the production of phantoms for the validation of image-guided navigation procedures.
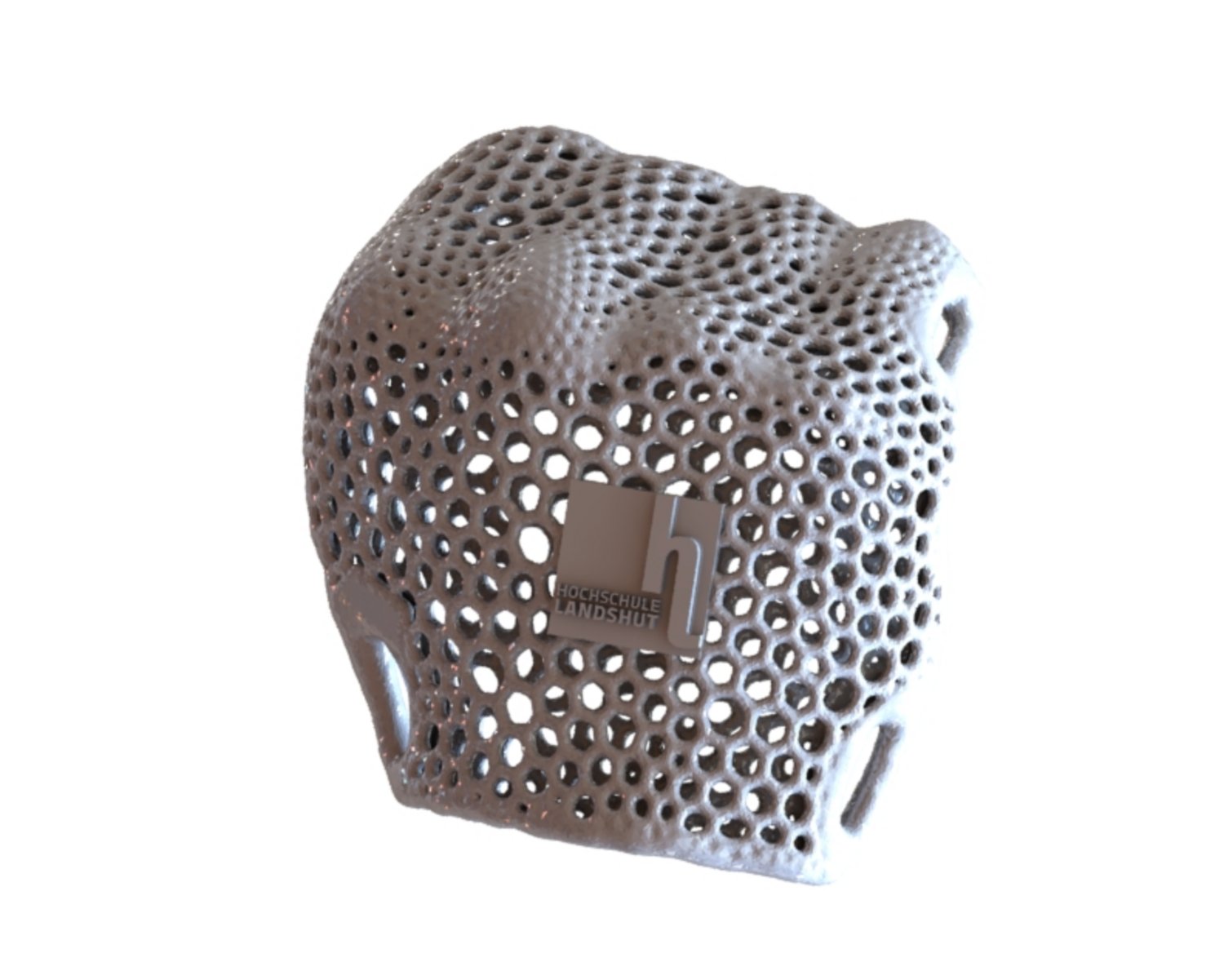
3D printing for orthopaedic surgery
Contact: Prof. Dr. N. Babel, Prof. Dr. S. Remmele
Partner: Dr Helmut Ersch, Orthopaedics, Agatharied Hospital
Bachelor's thesis Edith Gramotke (2021)
Various methods are currently being researched in medical technology to adapt implants to the anatomy in advance, either on virtual bone structures or using 3D-printed models.
The project developed a process for generating patient-specific 3D prints that can be used for preoperative implant adjustments. Planning before the operation shortens the operation time, as the implant shape no longer has to be optimised several times during the operation. This means less blood loss for the patient and therefore a faster recovery and a shorter hospital stay. Both the process for segmenting the CT data and for 3D printing have been optimised and evaluated in collaboration with Agatharied Hospital. To date, several operations have already been planned in this way, saving around 45 minutes of operating time according to the doctors. Edith Gramotke and Landshut University of Applied Sciences were awarded the Innovation Prize of the Scientific Society for Hospital Technology 2022(more).
Forearm crutch
Contact: Prof. Dr Norbert Babel, Prof. Dr Raimund Kreis
Project partner: Björn Furche (Ossenberg GmbH)
Bachelor theses: Veronika Selmaier (2022), Asena Kus (2023)
Walking aids such as forearm crutches in accordance with DIN EN ISO 11334-1 are often used for short periods after accidents or injuries. However, demographic change and increasing life expectancy mean that they are likely to be used for many years to come. This is because crutches can make a valuable contribution to maintaining mobility into old age. To increase acceptance, however, the walking aid must be optimally adapted to the respective user in terms of ergonomics and comfort. In addition, the image must change from that of a crutch - colloquially used to describe any form of half-baked makeshift device - to that of a stylish accessory.
The customisability of existing solutions is often still limited to length adjustability. However, a trend towards a greater variety of colours and shapes is already discernible. The aim of this project is to use additive manufacturing processes, for example, to customise forearm crutches more closely to the individual needs and wishes of the user. This concerns, for example, the geometry, colours and shapes of the crutches as well as the integration of additional functions.he company EBM Papst in Landshut over 40 Cardboard headsets!(Video)
KREIS, R. Customised forearm crutches - time and cost savings through the use of additive manufacturing [online]. 2023.(Link) [Last accessed 08.03.2023]
KREIS, R., V. SELMAIER and N. BABEL. Individualised forearm crutches. Design & Development. 2022. no. 5, p. 28-31.(link) [Last accessed 27/09/2022] .
KREIS, R., V. SELMAIER and N. BABEL. Customised production of forearm crutches using 3D printing. Management & Hospital. 2022. no. 4, p. 13.(link) [Last accessed 27.09.2022]
Opus
Hand Orthoses
Norbert Babel, Prof. Dr.-Ing. Raimund Kreis
Project partner: Dr Helmut Ersch, Agatharied Hospital
Bachelor's thesis: Nicolas Dietz (2023)
Orthoses are often used after injuries or illnesses to support the healing process. Orthoses enclose parts of the body in order to relieve and/or immobilise them.
In some cases, orthoses with standard geometries are not sufficient and must be customised to the patient. Moulds or casts on the patient can be uncomfortable or even painful due to the physical contact and the length of time the patient has to remain in a certain position.
The aim of the project is to develop methods that can be used to produce customised hand orthoses in a way that is gentle on the patient and requires as little effort as possible, possibly even directly in a medical facility. At the same time, it will be investigated whether CAD programmes can be used to model standard orthoses that can be 3D printed on demand.